Tube Forming
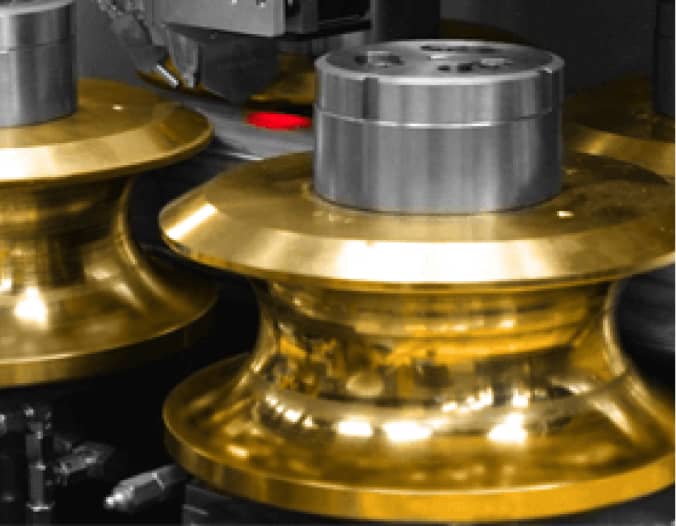
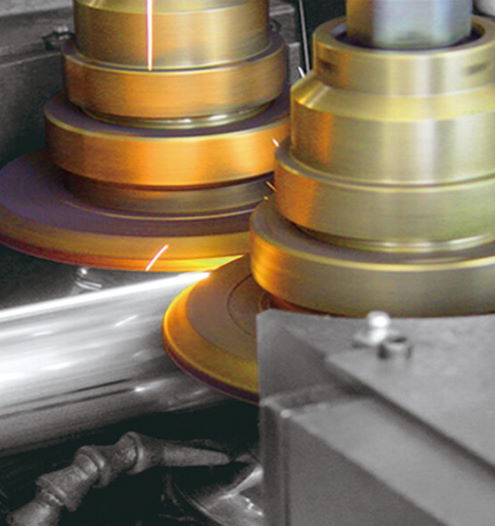
Tube forming means the process of shaping a flat piece of metal into a closed tube. Compared to tube bending, where the finished tube already is enclosed, but still needs to be bent into the final shape. Both, tube forming and tube bending, are metal forming processes.
Tube manufacturing and profile manufacturing
Two subsectors of metal forming are tube manufacturing and profile manufacturing. In order to produce tubes, pipes, and profiles of such nature, different mills are used to automate the process. These include in particular stainless steel tube mills, titanium tube mills, and roll forming mills.
What are roll forming mills?
In order to shape sheet metal into the desired shape, roll forming mills are used. These include a coil feeder, forming rolls, and welding rolls. The coil feeder is responsible for feeding the material – often coiled steel but not exclusively – through the process. Subsequently, the strip of sheet metal is passed through a set of forming rolls, where the metal is gradually shaped to prevent excessive stress. Furthermore, the progressive shaping prevents spring back from occurring.
When the roll forming mill is used to produce enclosed tubes, a welding station comes into play. This station is placed roughly in the middle of the roll forming mill and joins the two endings of the sheet metal together. Responsible for the welding are small welding rolls inside the welding station. The welding process used depends on the material of the tube. High-frequency induction welding uses a high-frequency current to melt the joining pieces together. Laser welding uses a laser beam to form the weld. And TIG welding includes the use of a non-consumable tungsten electrode to produce the weld.
Advantages of roll forming mills?
The advantages of a roll forming mill are obvious: It is highly suitable for mass production, thus making it the most economical production process for continuous bending – especially for difficult shapes. Therefore the roll forming process can increase efficiency while keeping the costs low. Furthermore, additional manufacturing processes – for example, punching – can be combined with the roll forming process to further enhance productivity.
Another advantage is the precision of the process. Thanks to roll forming mills, very tight tolerances can be met, which ultimately leads to a high consistency and therefore very high-quality end products. Other advantages include its flexibility and its cost-effectiveness.
Which tools are involved in roll forming
There are two key components when it comes to tube forming.
- Forming rolls
Forming rolls are basically precision-contoured metal dies that shape the incoming piece of sheet metal piece by piece until it reaches its desired shape. Depending on the complexity of the end product, they may be very simple cylindrical rolls – or highly complex. The forces acting on the rolls during the forming process can become very large. The rolls must defy these forces to guarantee a long and efficient service life. Therefore manufacturers need to be careful when choosing the right material for forming rolls. - Welding rolls
Welding rolls ensure that the ends of the original flat piece of metal are firmly welded together. They are pressed onto the tube during the welding operation. Multiple welding operations can be chosen: high-frequency induction welding (HFI), laser welding, or TIG welding. Depending on the welding operation, different properties are needed. In general, good sliding properties and high wear resistance are advantageous.
The role of aluminum bronze in tube forming
As the tube forming tools need to have certain characteristics in order to grant a long service life and high productivity, not every material is equally suited for the operation. When it comes to forming rolls, aluminum bronze is a perfect match as a tooling material because it combines good sliding properties, high hardness, and low elongation. These three properties are crucial when it comes to forming rolls.
Welding rolls, too, need to have specific characteristics. However, it is slightly more complex, due to the fact, that the welding technique may vary. But generally speaking, aluminum bronze is a great fit for any welding rolls. Particularly, AMPCO® 18, AMPCO® 21, AMPCO® 22, and AMPCO® 25.
Advantages of AMPCO alloys
Thanks to the MICROCAST® technology, AMPCO METAL delivers a wide range of superior materials that exceed the highest requirements. One of those is AMPCO® 25 as it offers multiple advantages in use and application, especially for welding rolls, forming rolls, and calibration rolls. Generally speaking, all AMPCO® alloys offer:
- Very good sliding characteristics
- No cold welds on the forming rolls
- Perfect surface on carbon, stainless steel, or titanium tubes
- No hardening or expensive coatings on the rolls required
- Easy to regrind with less power consumption in HF welding
AMPCO METAL has developed alloys that are highly suitable for all sorts of tube forming tools. For help determining the alloy and the product that best meets your needs, download our technical paper or contact our technical experts.