Wear Resistance
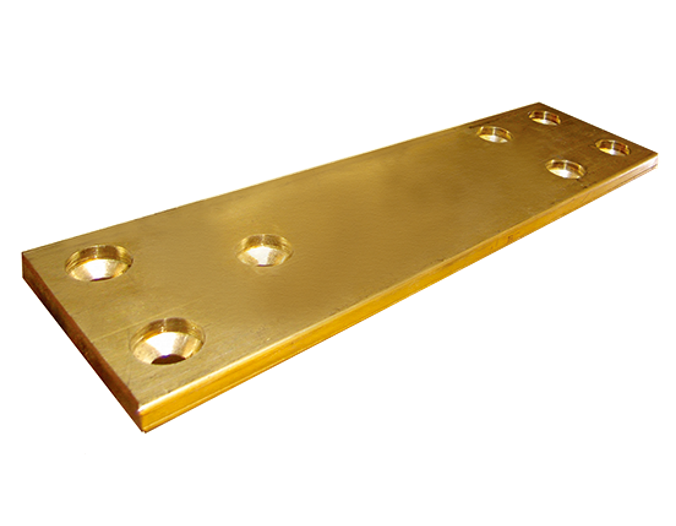
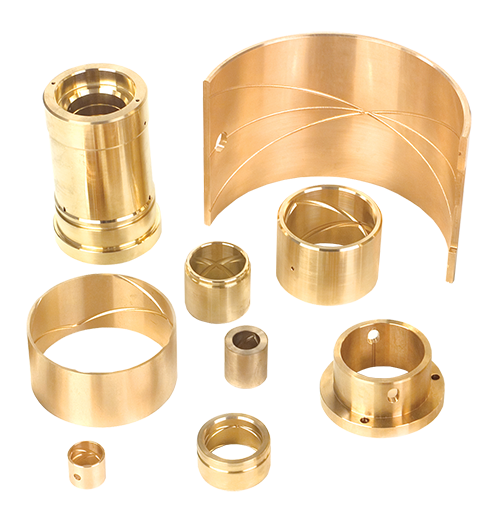
What is Wear resistance?
Wear is a natural phenomenon that occurs when two sliding surfaces interact with each other under load, ultimately resulting in a progressive loss of material. Therefore, wear is defined as the removal of material from a solid surface due to mechanical action exerted by another solid.
The wear resistance of a material indicates how resistant an alloy is to this process. The more wear-resistant an alloy, the less quickly it loses material from its surface. As wear is one of the main reasons for downtimes, using wear-resistant materials can increase productivity in steel mills and other industries.
Strictly speaking, wear is mechanical abrasion. This means that whenever two materials collide and rub against each other, mechanical abrasion occurs. This sort of abrasion always results in a loss of material thickness because friction constantly removes material from the surface of an object. A typical example of such a process is braking. But besides braking, an example of abrasive wear, there are other wear types.
What is wear, and what are its types?
Abrasive wear: Abrasive wear is caused by friction between two component surfaces, which causes particles to be rubbed off on the surface.
Surface fatigue: Surface fatigue is a wear mechanism caused by alternating mechanical stresses and causes pits to form.
Fretting: Fretting is corrosion intensified by a mechanical action: It involves consistent damage to the passive layer of a metal or alloy, resulting in accelerated corrosion of the unprotected surface.
Erosion: Erosive wear is caused by short sliding motion in a very short time interval, where the material is continuously removed from the surface by impact, deformation, and damage caused by exposed particles.
There are multiple ways to protect against wear. Lubrications form one solution. Another possibility is to improve the material properties to have the highest possible wear resistance. One material, in particular, comes to mind when there is a need for high wear resistance: Aluminum bronze!
Difference between corrosion and wear resistance
Corrosive wear can include any of the subtypes mentioned above. The difference is, that corrosive wear occurs only in a corrosive environment – typically in moist air, hot air, polluted air, hot water, acids, and salt water, among others.
Wear resistance of aluminum bronze
Due to its high tensile strength in combination with a low coefficient of friction when mated with moving elements made of hardened steel, aluminum bronze is hard to beat when it comes to wear resistance. Furthermore, the alloy can function even under very high temperatures and is perfectly suited for harsh environments. There are multiple wear applications where aluminum bronze is beneficial regarding its wear resistance. For example, brake pads for roller coasters, worm gear wheels, wear plates, bearings, and all types of friction applications.
There are many other wear applications where the unmatched properties of the AMPCO® alloys are beneficial. The secret behind our alloys’ superior wear capabilities lies in their production. Our unique MICROCAST® manufacturing process allows for optimal grain size, density, and dispersion control, contributing to the rugged wear resistance of AMPCO® alloys.
Furthermore, our AMS alloys are specially designed for the challenging field in the aerospace industry. The so-called aerospace bronze is typically used for parts and landing gears and provides characteristically high-strength and mechanical properties beyond the range of commercial aluminum bronzes.